History of black steel pipe
William Murdock made the breakthrough leading to the modern process of pipe welding.In 1815 he invented a coal burning lamp system and wanted to make it available to all of London. Using barrels from discarded muskets he formed a continuous pipe delivering the coal gas to the lamps. In 1824 James Russell patented a method for making metal tubes that was fast and inexpensive. He joined the ends of flat iron pieces together to make a tube then welded the joints with heat. In 1825 Comelius Whitehouse developed the “butt-weld” process, the basis for modern pipe making.
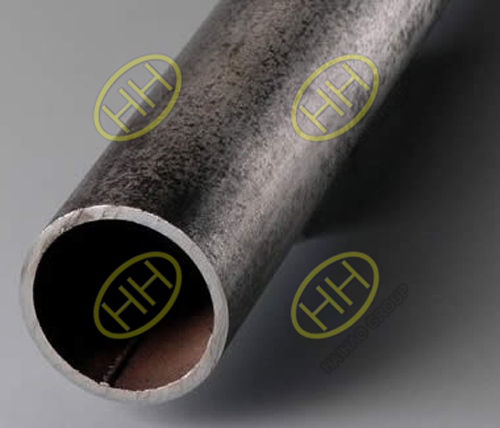
Black Steel Pipe
Developments of black steel pipe
Whitehouse’s method was improved upon in 1911 by John Moon. His technique allowed manufacturers to create continuous streams of pipe. He built machinery that employed his technique and many manufacturing plants adopted it. Then the need arose for seamless metal pipes. Seamless pipe was initially formed by drilling a hole through the center of a cylinder. However, it was difficult to drill holes with the precision needed to ensure uniformity in wall thickness. An 1888 improvement allowed for greater efficiency by casting the billet around a fire-proof brick core. After cooling, the brick was removed, leaving a hole in the middle.
Applications of black steel pipe
Black steel pipe’s strength makes it ideal for transporting water and gas in rural and urban areas and for conduits that protect electrical wiring and for delivering high pressure steam and air. The oil and petroleum industries use black steel pipe for moving large quantities of oil through remote areas. This is beneficial, since black steel pipe requires very little maintenance. Other uses for black steel pipes include gas distribution inside and outside homes, water wells and sewage systems. Black steel pipes are never used for transporting potable water.
Modern Techniques of black steel pipe
Scientific advancement has greatly improved on the butt-weld method of pipe making invented by Whitehouse. His technique is still the primary method used in making pipes, but modern manufacturing equipment that can produce extremely high temperatures and pressure has made pipe making far more efficient. Depending upon its diameter, some processes can produce welded seam pipe at the incredible rate of 1,100 feet per minute. Along with this tremendous increase in the rate of production of steel pipes came improvements in the quality of the final product.
Quality Control of black steel pipe
The development of modern manufacturing equipment and inventions in electronics allowed for marked increases in efficiency and quality control. Modern manufacturers employ special X-ray gauges to ensure uniformity in wall thickness. The strength of the pipe is tested with a machine that fills the pipe with water under high pressure to make sure the pipe holds. Pipes that fail are scrapped.
If you would love to know more professional information ,or enquiry,please send email to me:sales@haihaogroup.com