There are mainly two methods to manufacture the flanges: forging and casting.(The difference between forging and casting)
Cast flange is a lower cost flange and suitable for medium or low pressure pipelines. It has below features:
- High production efficiency and low production cost.
- Could made to a more complicated shape and with lower a cost.
- The blank shape and size of cast steel flange is accurate, the processing quantity is small.
- Have casting defects, such as porosity, crack, inclusion.
- The internal flow of the casting is slow.
- If it is a cutting part, the streamline type is worse.
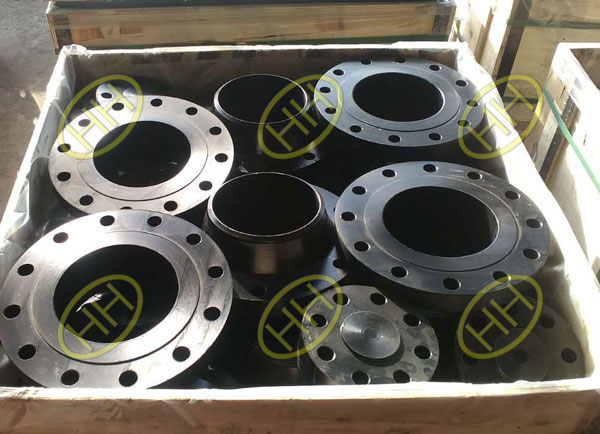
ASTM A350 LF2 Weld Neck Flanges In Haihao Group
Forged steel flange has higher precision and performances than the cast flange and widely used in different industries for connecting equipment or pipelines, especially for high temperature and high pressure environments.
Forged flange is a plate-type device, usually in circular appearance which could be attached the ends of pipes, fittings, valves or other objects to facilitate assembly and dis-assembly of the piping system. It offers impressive mechanical performance as a connecting parts.
- Forged flange generally has lower carbon content than cast iron flange, so they are not easy to rust.
- It has good streamline shape and compact structure, so their mechanical properties are better than cast flange.
- If the forging process is improper, the grain will be large or uneven, and the hardening crack will occur. The cost of forged steel flange is higher than that of the casting flange.
- Forgings is compatible with higher shear and tensile forces than castings.
- The internal structure of the forging is uniform, and there are no harmful defects such as pores and inclusions in the casting.
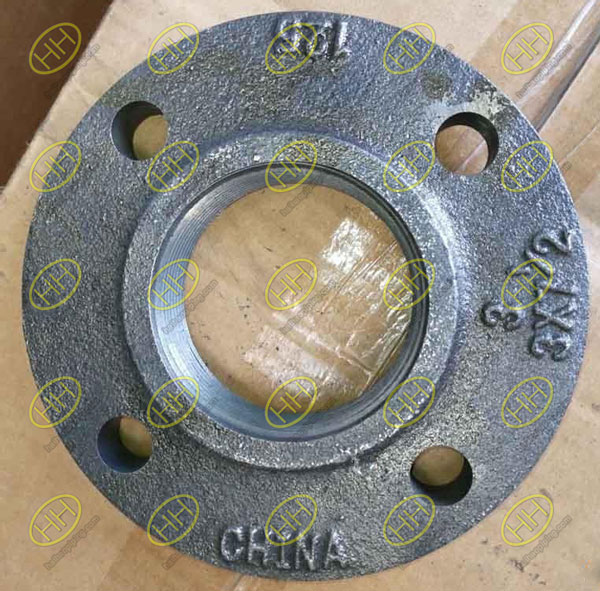
Casting Threaded Flange