As a leading expert in pipeline systems and prefabricated welded components, Haihao Group frequently assists global clients with welding-related solutions. With decades of experience, we’ve developed deep insights into welding processes, including the correct use of DCEN (Direct Current Electrode Negative) and DCEP (Direct Current Electrode Positive)—commonly known as straight polarity and reverse polarity, respectively.
Understanding the differences between these two setups is essential for achieving optimal welding results, especially when working with a wide range of metals and alloy materials.
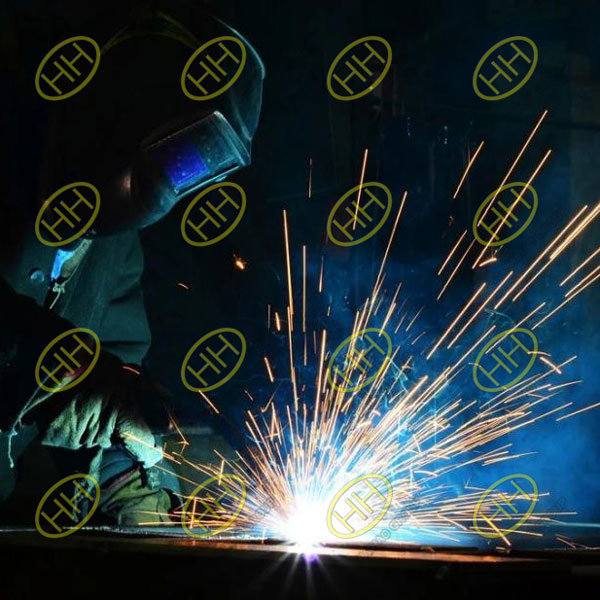
DCEN in Welding
What is DCEN (Straight Polarity)?
DCEN (Direct Current Electrode Negative), also referred to as straight polarity, connects the electrode to the negative terminal and the workpiece to the positive terminal. In this configuration, most of the heat is concentrated on the workpiece, allowing for deeper penetration and faster welding.
In high-frequency testing such as the Wheatstone Bridge method for measuring dielectric loss factors, straight polarity is also used to minimize surface resistance interference—making it effective for certain testing environments.
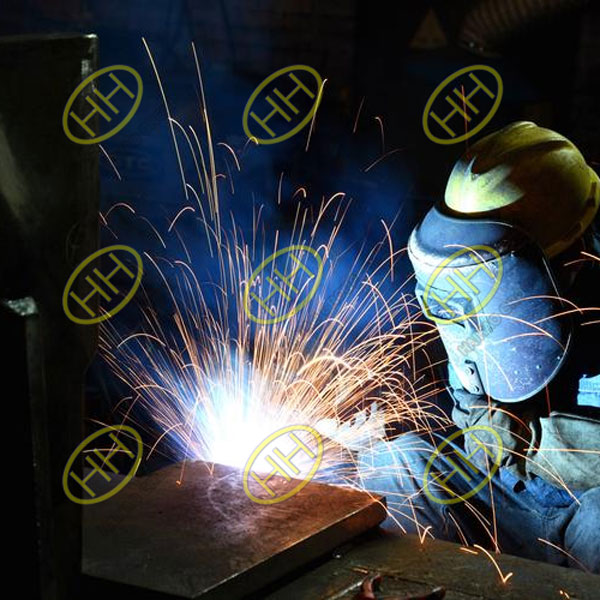
DCEP in Welding
What is DCEP (Reverse Polarity)?
DCEP (Direct Current Electrode Positive), or reverse polarity, connects the electrode to the positive terminal and the workpiece to the negative terminal. This method is especially useful in TIG (GTAW) welding of reactive metals like aluminum and magnesium.
Why? Because DCEP supports the “cathodic cleaning” effect, which helps break down the oxide layer that naturally forms on the surface of these metals. This effect—also referred to as cathode sputtering or cathodic etching—is critical for producing clean, bright, and visually appealing welds.
Choosing the Right Polarity for Your Weld
The choice between DCEN and DCEP depends on:
Base material type
Oxide layer characteristics
Penetration requirements
Weld aesthetics
For example, when welding aluminum alloys, DCEP or alternating current (AC) is often used to remove oxide films and ensure weld quality. In contrast, DCEN is better suited for carbon steel and other ferrous metals, where deeper penetration is desired.
Haihao Group’s Welding Expertise
At Haihao Group, our dedicated technical team evaluates every welding task based on the material and performance requirements. Whether it’s carbon steel, stainless steel, or special alloy piping, we apply the most appropriate welding methods—including correct polarity setup—to ensure:
- High-quality weld seams
- Strong mechanical performance
- Precise fit-up for prefabricated pipe assemblies
We also conduct on-site testing and adopt best welding practices to meet international standards and client-specific requirements.
If you’re looking for a trusted partner in industrial piping and custom welding solutions, Haihao Group is ready to support your project with proven expertise and advanced welding technology. Email:sales@haihaogroup.com