The welding methods of pipes mainly include resistance welding (ERW), l0ngitudinal-seam submerged arc welding (LSAW) and spiral submerged arc welding (SSAW). These methods are described below:
ERW can be divided into induction welding and contact welding two forms. Compared with spiral welding, ERW is made of wide roll hot rolling material, prebending, continuous molding, welding, heat treatment, sizing, straightening, cutting, etc. It has the advantages of high dimensional accuracy, uniform thickness, surface quality and pressure, but the disadvantage is that it can only produce medium and small diameter thin-wall pipe, and the weld is easy to produce gray spots, not easy to fuse groove corrosion defects. It is widely used in urban gas and crude oil transportation.
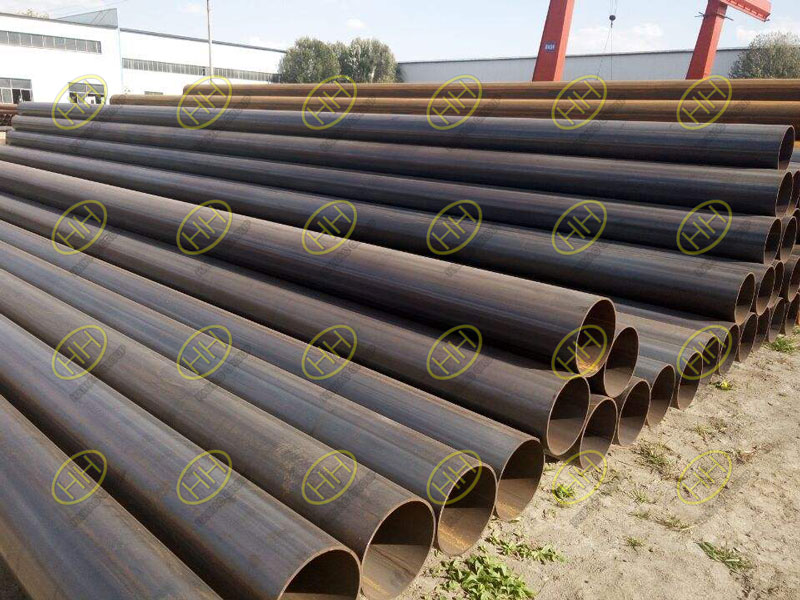
Electric resistance welded steel pipes ERW steel pipes
SSAW pipes are made of hot rolled coil steel through automatic submerged arc welding at room temperature. These pipelines are primarily used in the oil and gas industry to transport flammable and non-flammable liquids and steel structures.
Spiral welded steel tubes are widely used in the transportation and distribution of petroleum, natural gas, water and other flammable and non-flammable liquids due to their wide range of dimensions, construction steel structures and other general purposes.
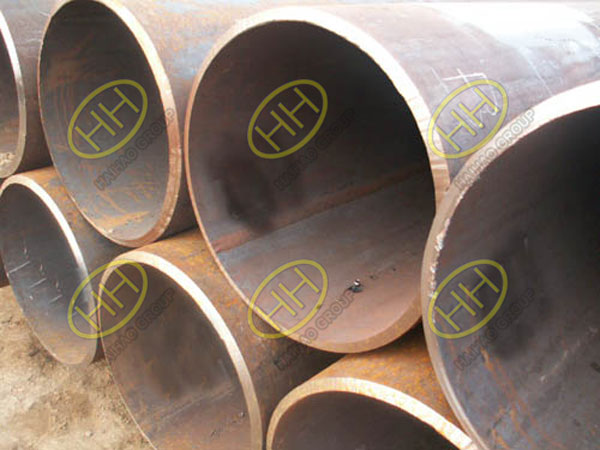
Longitudinal seam Submerged Arc Welded (LSAW) pipes
LSAW is produced in a mold or molding machine by using double submerged arc welding and raw material flaring. The finished product has a wide range of specifications, good weld toughness, ductility, uniformity and density, large diameter, wall thickness, high pressure resistance, low temperature corrosion resistance and other advantages. In the construction of high strength steel pipe, the long distance oil and gas pipeline with high toughness and high quality is mostly large diameter thick wall LSAW.
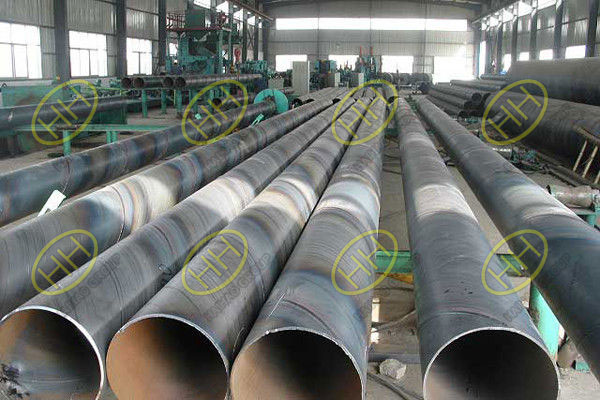
Spiral submerged arc welding (SSAW) steel pipes