We know the heat treatment processes contain quenching, tempering, normalizing,here is the last step of the heat treatment process-annealing.
What is annealing?
Annealing is a metal heat treatment process that slowly heats the metal to a certain temperature, holds it for a sufficient time, and then cools it down at a suitable rate. Annealing heat treatment is divided into complete annealing, incomplete annealing and stress relief annealing. The mechanical properties of the annealed material can be tested by tensile tests or hardness tests. Many steels are supplied in annealed and heat-treated state. The hardness of steel can be tested using Rockwell hardness tester to test HRB hardness. For thinner steel plates, steel strips and thin-walled steel pipes, surface Rockwell hardness tester can be used to test HRT hardness.
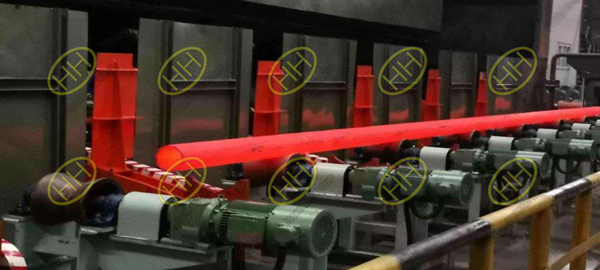
Annealing of steel tube
The purpose of annealing is to:
① Improve or eliminate various structural defects and residual stress caused by steel in the process of casting, forging, rolling and welding, and prevent workpiece deformation and cracking
② Soften the workpiece for cutting.
③ Refine the grains and improve the structure to improve the mechanical properties of the workpiece.
④ Prepare the structure for final heat treatment (quenching, tempering).
Common annealing processes are:
① Completely annealed. It is used to refine the coarse superheated structure with poor mechanical properties after casting, forging and welding of medium and low carbon steel. The workpiece is heated to a temperature of 30-50 ° C above the temperature at which ferrite is completely transformed into austenite, and is held for a period of time, and then slowly cooled with the furnace. During the cooling process, the austenite is transformed again to make the structure of the steel finer .
② Spheroidizing annealing. To reduce the high hardness of tool steel and bearing steel after forging. The workpiece is heated to a temperature between 20 and 40 ° C above the temperature at which the steel begins to form austenite, and then slowly cooled after the heat preservation. During the cooling process, the lamellar cementite in the pearlite becomes spherical, thereby reducing the hardness.
③ Isothermal annealing. Used to reduce the high hardness of some alloy structural steels with higher nickel and chromium content for cutting. Generally, it is first cooled to the most unstable temperature of austenite at a relatively rapid rate, and after holding for an appropriate time, the austenite is transformed into toustenite or sorbite, and the hardness can be reduced.
④ Recrystallization annealing. It is used to eliminate the hardening phenomenon (increased hardness and decreased plasticity) of metal wires and sheets during cold drawing and cold rolling. The heating temperature is generally 50 to 150 ° C below the temperature at which the steel begins to form austenite. Only in this way can the work hardening effect be eliminated and the metal softened.
⑤ Graphitized annealing. Used to make cast iron containing a large amount of cementite into malleable cast iron with good plasticity. The technical operation is to heat the casting to about 950 ° C, and then cool it properly after holding for a certain period of time to decompose the cementite to form flocculent graphite.
⑥ Diffusion annealing. It is used to homogenize the chemical composition of alloy castings and improve its performance. The method is to heat the casting to the highest possible temperature without melting, and keep it warm for a long time, and then slowly cool after the various elements in the alloy tend to be uniformly distributed.
⑦ Stress relief annealing. To eliminate the internal stress of steel castings and weldments. For steel products, the temperature at which austenite starts to be formed is 100 to 200 ° C below the temperature, and after cooling, the internal stress can be eliminated by cooling in air.