As we all know LSAW steel pipes are widely used in many industries,do you know the production method of large diameter LSAW steel pipe?Now let me tell you about it.
Production process introduction of large diameter LSAW steel pipe
Rolling machine→Uncoiler→Unwinder→Retripper leveling machine→Vertical roll centering→Shear butt welding→Strip position control (double-head vertical roller)→Disc shearing→Strip position control (Double-head vertical roller )→ Edge Milling Machine (Fine Milling X Groove)→ Double End Roller→ Strip Surface Cleaning of Strips→ Double End Roller→ Conveyer→ Strip Feeding and Strip Position Control→ Molding Machine→ Inner Welding→ Outside Welding → steel pipe righting device → plasma cutting → straight seam steel pipe outlet
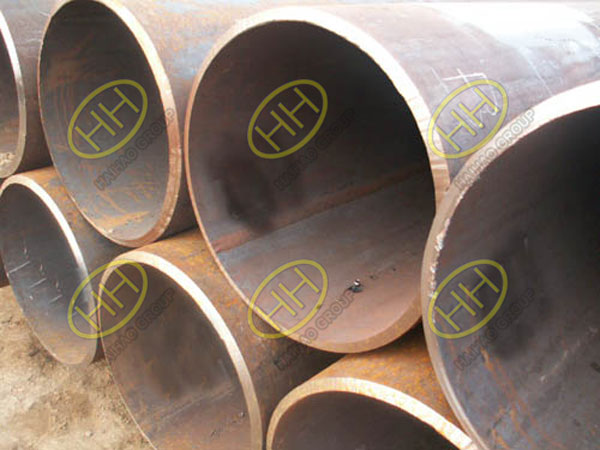
Longitudinal seam Submerged Arc Welded (LSAW) pipes
Production process details of large diameter LSAW steel pipe
1.Work before forming
Raw materials are steel coils, welding wire, and flux. Have to go through rigorous physical and chemical tests before investing. The butt joints of the steel strips are welded with monofilament or double wire submerged arc welding. After the steel tube is rolled, automatic submerged arc welding is used for welding.
2.Molding process
The electric contact pressure gauge is used to control the pressure of the compression cylinders on both sides of the conveyor to ensure the smooth delivery of the strip. The main machine is positioned at the center. Therefore, the adjustment of the vertical roller (especially before and after the head) should be checked frequently to ensure the strict delivery edge of the strip. Run on the route specified by the process and pass the designed meshing point. External control or internal control roll forming is used to check whether the perimeter, ellipticity, straightness, etc. of the steel pipe comply with the standard requirements. If it does not meet the requirements, it will continue to be adjusted until it meets the requirements.
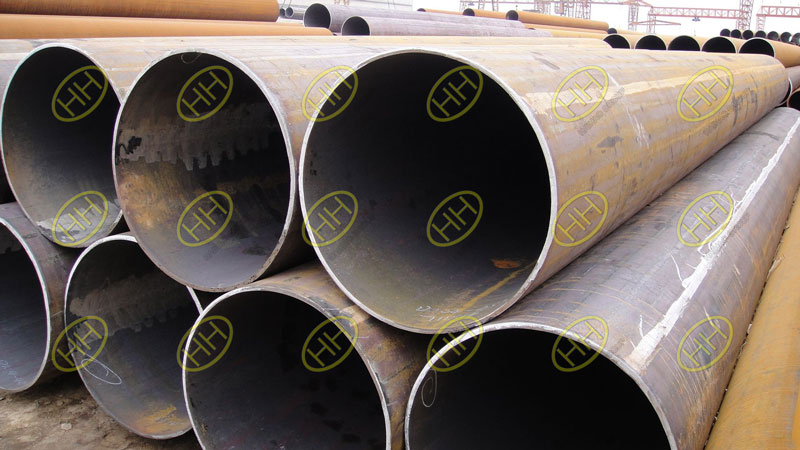
Double surface straight seam submerged arc welding steel pipes
3.Welding process
The weld gap control device is used to ensure that the weld gap satisfies the welding requirements. The pipe diameter, the amount of misalignment, and the weld gap are all strictly controlled. The quality of the forming seam should be observed continuously, and it should be found that the misaligned edges, open seams, etc. Fine-tune the angle of the rear axle in time to ensure the quality of the forming; when the situation is abnormal, check whether the working width of the strip, the pre-bending condition of the edge, the position of the delivery line, the angle of the small roller, etc. have changed, and take corrective measures in time. Hebei’s straight seam steel pipe manufacturers currently use the United States Lincoln welding machine for single wire or double wire submerged arc welding in order to obtain stable welding quality. Straight seam steel pipe manufacturers shall continuously observe the quality of the forming joints, and shall promptly fine-tune the rear axle angle to ensure the molding quality in the case of misaligned edges, open seams, etc.; if the conditions are abnormal, check the working width, edge pre-bending condition, and delivery of the steel strip. Whether there is any change in the line position, the small roller angle, etc., and take corrective measures in time.
4.Detection
The welded welds were all inspected on-line by an automatic ultrasonic flaw detector to ensure 100% non-destructive inspection coverage of the spiral weld. If there are defects, they will be automatically alarmed and painted. The production workers will adjust the process parameters at any time to eliminate defects in time. When the nominal diameter D ≥ 426mm, the internal defects of the steel pipe should be cleaned and repaired inside; when D ≤ 426mm, the internal defects can be removed from the outside to perform the external welding. After repair welding, the weld must be ground and the remaining wall thickness after grinding should be within the specified wall thickness tolerance. Before repairing the welded steel pipe into the next process, it is necessary to carefully inspect whether there is any missing or missed defect on the steel pipe and correct it before proceeding to the next process. The butt-welded joints of the steel butt-welded joints and the spiral welds were all examined by X-ray television or film. Each pipe was hydrostatically tested and the pressure was radial sealed. The test pressure and time are strictly controlled by the steel pipe hydraulic pressure testing device. Test parameters are automatically printed and recorded.(Non-destructive testing of LSAW steel pipe)
5.Packaging out of the library
Pipe end machining, so that the end face perpendicularity, groove angle and blunt edge are accurately controlled. An air plasma cutter cuts the steel tube into individual pieces. After the blade is blunt or damaged, the new blade should be replaced immediately. The new blade must be sharpened with a stone before use, and it must not be ground with a grinder. After the blade is broken, it can be used after applying grinding stone again after grinding with a grinder.
If you would love to know more detail,please contact us.Email:sales@haihaogroup.com