Global trends in pipeline technology and pipeline coatings are in part dictated by where the oil and gas reserves are located. These reserves are becoming increasingly difficult to find. Producers are looking further afield and often find the reserves are much deeper than in the past. Associated with this, the resources tend to flow under high temperatures and pressures. The pipelines may also need to be constructed in remote and harsh environments.So it is necessary for us to learn the pipeline coating types in high temperature.
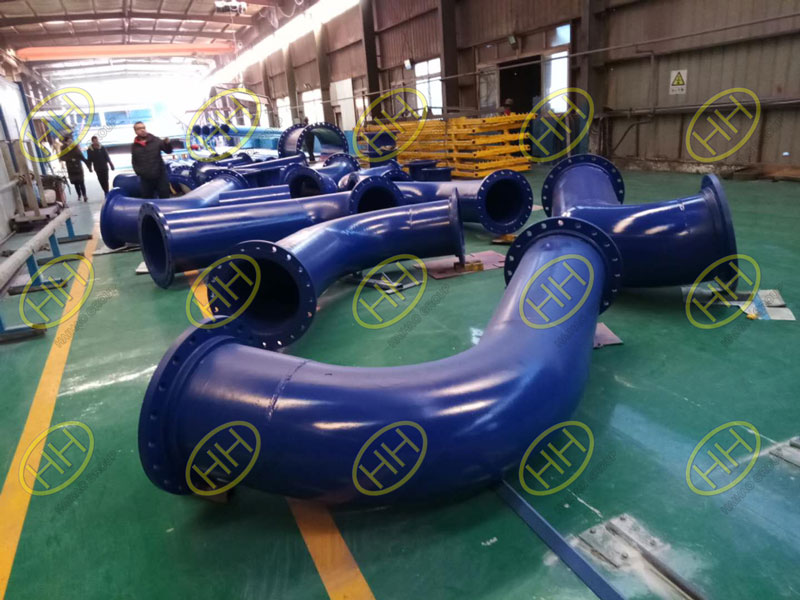
FBE Coating Pipings
High performance pipeline corrosion protection coatings have been developed to meet the demanding requirements of current pipeline engineers. A variety of pipeline-coating technologies are available, and selection has evolved along geographical lines.
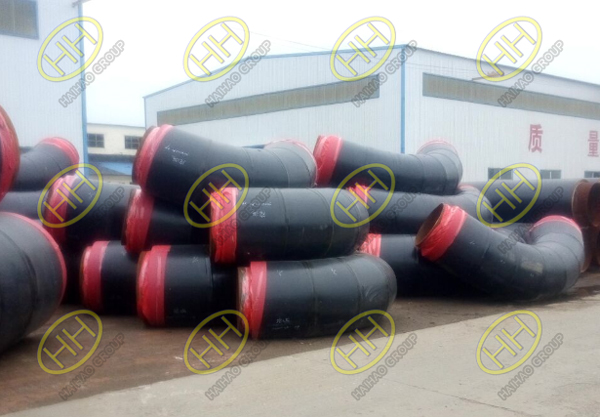
Mitre Bend with 3LPE
In North America, fusion bonded epoxy (FBE), and 2-layer polyethylene (2LPE) have been the dominant coatings, although accelerating acceptance of multi-layer coatings is being noted. In Europe, Asia, Middle East and South America, multi-layer polyolefin coatings such as 3-layer polyethylene (3LPE) and 3-layer polypropylene (3LPP) tend to be favoured. Also, newer technologies such as composite coatings (HPCC) and multi-layer, insulated systems are gaining attention.The table below examines commonly available coatings and their typical maximum operating temperatures.
Speciality
Coating Type | Maximum Operating Temperature |
Fusion Bonded Epoxy (FBE) | 85 – 90ºC |
2-Layer Polyethylene (2LPE) | 60ºC |
3-Layer Polyethylene (3LPE) | 85 – 90ºC |
3-Layer Polypropylene (3LPP) | 110 – 140ºC |
Composite Coatings (HPCC) | 85ºC |
*Data gathered from pipe coating companies’ published literature. Speciality grades of raw materials may be rated higher
Haihao Group is committed to provide different piping solutions for clients.If you have any problems for the piping problems,contact us freely.Email:sales@haihaogroup.com