There are many production processes for stainless steel pipes, and the finished products are bundled very neatly, and the surface of stainless steel pipes are also very beautiful. How does the manufacturing process the surface of the stainless steel pipe during production?
When producing stainless steel pipes, it is necessary to pay attention to all aspects. The grinding and surface machining of stainless steel pipes requires careful and careful attention. With the wider use of stainless steel pipes, more manufacturers will have larger orders, they must not be careless, and they must handle the surface of stainless steel pipes. Speaking of the surface treatment of stainless steel pipe, the first thing to mention is the grinding process, which is part of the polishing process.
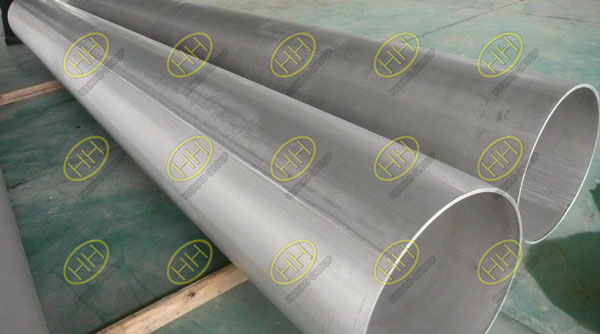
Duplex S31803 2205 welded pipes
In fact, there are many tricks in the surface treatment of such stainless steel pipes. If there are defects on the surface of the stainless steel pipe, it is necessary to grind it manually at this time, and then make a decision on the bar. Stainless steel pipes have now been effectively applied to many fields, and their chemical properties are different from those of other stainless steel materials.
For surface treatment of stainless steel pipes, the workpiece must be inspected in all directions. If quality is found to be unacceptable, such as incomplete mating, uneven solder joint depth, etc., it is best to rework until stainless steel pipe work is confirmed to be defective. Polished. In the process of sanding the stainless steel pipe, it is necessary to carefully remove the solder joints and scratches left by the welding, so that the surface treatment is clean. There are two types of grinding: rough grinding and fine grinding. After grinding, the workpiece surface of stainless steel pipe will be very bright, and can completely eliminate the traces of the joints. After polishing, the stainless steel pipework should exhibit a mirror-like effect.
Polishing is also a process for treating the surface of a stainless steel pipe. There are generally three methods, namely, mechanical polishing, chemical polishing, and electrochemical polishing. Mechanical polishing is particularly suitable for large-size polishing, where small parts are difficult to achieve very good results and are suitable for batch production. The advantage of this method is that it can perform surface treatment very well. However, its disadvantages are high investment costs, relatively large labor intensity, and serious pollution problems. Therefore, many manufacturers are not optimistic about this.
Chemical polishing is the same, its cost is low, there is no need to use large-scale mechanical equipment, the investment is flexible, and the polishing speed is very fast, but the disadvantage is that the brightness of the polishing is not good enough. The process of electrochemical polishing method is more stable, it is easy to operate, and the investment cost is lower, and the pollution is also small. Generally, once a one-time investment is no longer necessary, the cost is now used by most companies.