As a trusted supplier in the pipeline industry, the ability to provide durable, high-performance components like forged flanges is crucial for ensuring the efficiency, safety, and longevity of your pipeline systems. Understanding the advanced manufacturing technology and strict technical standards behind forged flanges can help demonstrate the value and reliability of your products to customers.
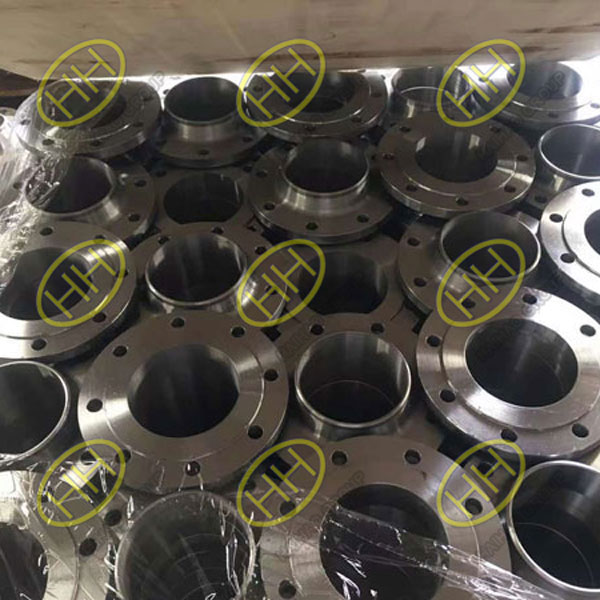
ASTM A105 Weld Neck Flanges
1. State-of-the-Art Forged Flange Manufacturing Process
Forged flanges are a cornerstone of piping systems, connecting pipes, valves, and other critical components with superior strength, reliability, and resistance to harsh environments. To achieve this, the forging process undergoes several high-precision steps designed to enhance the mechanical properties of the metal, ensuring that the final product can withstand extreme pressures and temperatures while offering a secure and leak-free connection.
Premium Material Selection:
The first step in producing high-quality forged flanges is the selection of raw materials. We source top-grade carbon steel, stainless steel, and alloy steel, each chosen to meet the specific requirements of the application, whether it involves high pressure, corrosive environments, or extreme temperatures. Each material is tested for chemical composition and mechanical properties before production.
Precision Forging:
Once the steel has been carefully selected, it is heated to the optimal forging temperature—typically between 900°C and 1250°C (1650°F to 2280°F). Under controlled conditions, the steel is subjected to powerful mechanical pressure through either open-die or closed-die forging techniques. This process shapes the flange while refining the metal’s grain structure, giving it enhanced strength and toughness—qualities that are essential for critical pipeline applications.
Accurate Machining and Tolerances:
After forging, each flange is machined with precision tools to ensure it meets exact dimensional specifications. Key operations include turning, drilling bolt holes, and finishing the sealing surfaces. These machining processes are crucial to ensuring perfect alignment during installation and maintaining the tight tolerances required for high-pressure and high-temperature systems. Advanced CNC machinery is employed to meet the strict requirements set by international standards such as ASME, DIN, and EN.
Controlled Heat Treatment:
For certain applications, especially those that involve extreme temperatures or pressures, heat treatment is a critical step. Processes like quenching, tempering, or normalizing are applied to adjust the flange’s mechanical properties, such as hardness, ductility, and impact resistance. This step ensures that the flange can maintain its integrity in demanding environments, including cryogenic or high-heat conditions.
Finishing and Surface Treatment:
To further enhance performance, forged flanges can undergo surface treatments such as galvanization, painting, or anti-corrosion coatings. These treatments are essential in protecting the flanges from rust, corrosion, or chemical degradation, especially in offshore or chemical processing environments.
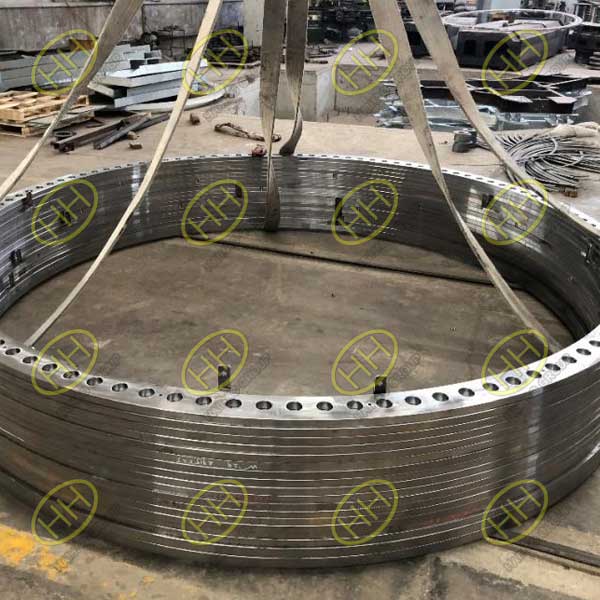
Large flange for wind power
2. Strict Technical Standards and Compliance
Meeting technical specifications is not just a requirement but a commitment to quality and reliability. Our forged flanges are manufactured in accordance with the highest industry standards, ensuring that they meet or exceed the demands of various industrial applications.
Pressure Rating and Dimensional Accuracy:
All our flanges are designed to meet the pressure ratings required by standards such as ASME B16.5, ASME B16.47, EN 1092-1, and others. These ratings—ranging from Class 150 to Class 2500 or PN ratings—ensure that the flanges can handle extreme pressures without compromising safety. Our advanced machining processes guarantee that all flanges are manufactured within the tightest tolerances, ensuring precise fit and performance.
Material Certifications:
Each flange is manufactured from materials that comply with ASTM and EN standards for carbon, stainless, and alloy steels. For example, ASTM A105 (for carbon steel) and ASTM A182 (for stainless and alloy steels) specify the required mechanical properties such as tensile strength, yield strength, and impact resistance. These certifications ensure that the materials used can withstand the operational stresses they will encounter in service.
Surface Finish and Gasket Compatibility:
The performance of a flange depends heavily on its sealing surface. We offer various sealing surfaces such as Raised Face (RF), Flat Face (FF), and Ring-Type Joint (RTJ) to suit different gasket materials and system requirements. The surface finish is controlled to ensure optimal gasket seating, preventing leaks in both low- and high-pressure environments.
Non-Destructive Testing (NDT) and Inspection:
To guarantee the structural integrity and reliability of each flange, we perform extensive testing during and after production. Non-destructive testing methods such as ultrasonic testing (UT), magnetic particle testing (MT), and dye penetrant testing (PT) are used to detect any internal or surface defects. Dimensional inspections, hardness tests, and pressure testing are also conducted to ensure that every flange meets the strictest quality requirements.
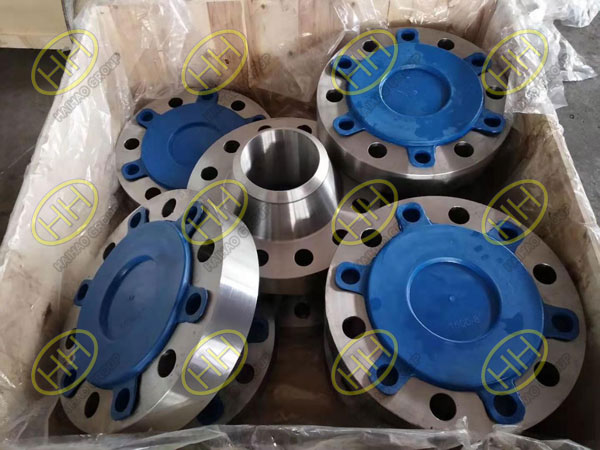
A694 F65 Long Weld Neck Flanges RTJ
3. Why Choose Our Forged Flanges for Your Pipeline Solutions?
By focusing on quality, precision, and technical expertise, our forged flanges deliver superior performance in even the most challenging environments. Here’s why we are the preferred partner for pipeline suppliers across various industries:
Customized Solutions:
We understand that each pipeline project comes with unique challenges. Whether it’s adapting to high-pressure, high-temperature environments, or dealing with corrosive chemicals, our engineering team works closely with customers to provide tailor-made solutions. From material selection to customized designs, we ensure that the flanges meet your exact operational requirements.
Superior Strength and Durability:
The forging process enhances the strength and toughness of the metal, providing better fatigue resistance compared to other manufacturing methods like casting. Our forged flanges are designed to withstand the repeated stresses of operation, ensuring long-term reliability even under fluctuating loads.
Cost-Effectiveness:
While forged flanges are known for their superior strength and durability, they also offer excellent value in terms of lifespan and reduced maintenance. High-quality materials and precise manufacturing ensure fewer system failures, reduced downtime, and lower repair costs—leading to long-term savings for pipeline operators.
Comprehensive Range and Availability:
We offer an extensive range of forged flanges, including weld neck, slip-on, blind, socket weld, threaded, and lap joint flanges. All products are available in various sizes, materials, and pressure ratings, ensuring that you can find the right flange for your project. Our manufacturing capabilities allow us to fulfill both small orders and large-scale industrial demands with short lead times.
Global Standards Compliance:
Our forged flanges comply with international standards such as ASME, API, DIN, and ISO, making them suitable for global projects across industries like oil and gas, petrochemicals, power generation, and water treatment. Whether your project is local or international, you can be confident in the quality and compliance of our products.
Whether you’re working on a high-pressure refinery, a chemical processing plant, or a critical water supply system, we have the expertise and capability to deliver the forged flanges you need to succeed.
For more information or to discuss your specific project requirements, please contact us today. Let us be your trusted partner in delivering high-performance forged flanges for all your pipeline needs.Email:sales@haihaogroup.com