In the plastic forming of forgings, the entire fracture process is a very complicated process. The fracture is not only related to the chemical composition, microstructure and initial defects of the material, but also has a great relationship with the processing technology, such as stress state, strain state, strain rate, although friction and forming temperature have a great influence on the forming quality of the material. In addition, material parameters such as strain hardening, void volume fraction, and second-phase particles all have an effect on the fracture of the material. The influence of stress-strain state, deformation temperature and other external factors on material fracture is as follows.
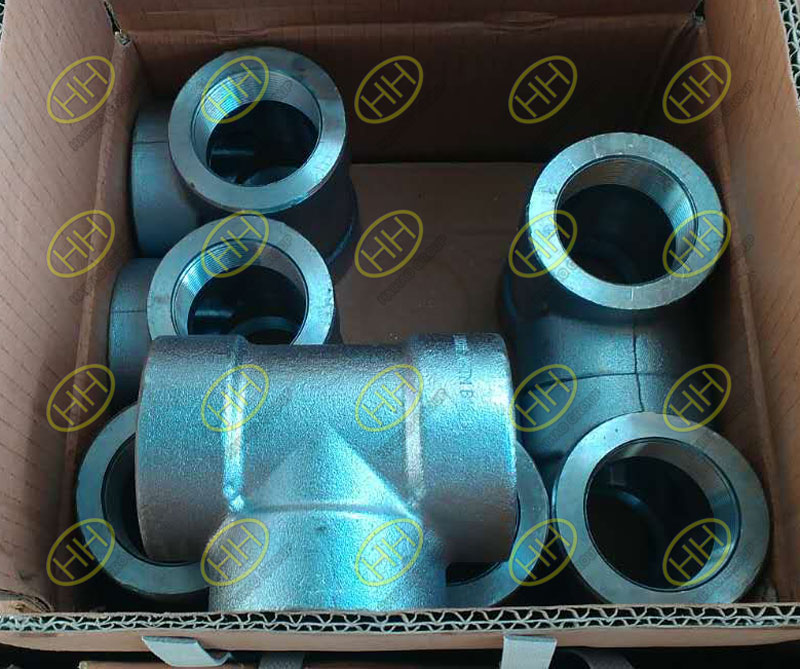
ASME B16.11 threaded equal tees
1. The influence of stress state on ductile fracture
A lot of industrial production and scientific research show that forgings can exhibit better plasticity under compressive stress and are less prone to ductile fracture failure. Generally, the hydrostatic stress is used to reflect the level of compressive stress in plastic theory. The smaller the hydrostatic stress, the better the plastic processing performance of the material during forming, such as the common upsetting and extrusion process; and the drawing of the forging material During the stretching process, the local hydrostatic stress of the forging is positive and the value is large, which is easy to cause fracture. In the process of cavity growth and polymerization, if the stress triaxiality is greater, the cavity grows faster, and when the tensile stress is small That is, when the stress triaxiality is small, the cavity growth and polymerization process will be slowed, thereby suppressing the occurrence of forging cracking.
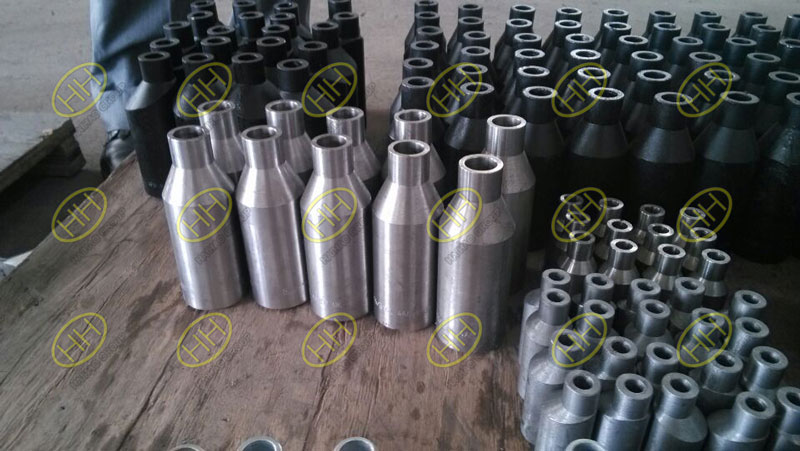
Concentric swage nipples and eccentric swage nipples
2. The influence of plastic deformation on ductile fracture
There is a critical value in the forming process of forgings. When the plastic deformation reaches this value, some small inclusions will break, or some second phase particles will separate from the body itself, or even generate micro-cavities. The micro-cavity will gradually grow and converge and merge, eventually leading to fracture. Studies have shown that the number of micro-cavities increases with the amount of plastic deformation, and slowly increases first (nearly linear relationship), and when the amount of plastic deformation reaches a certain critical value, the number of cavities will increase rapidly, and the rate of increase it is related to the properties of the material itself.
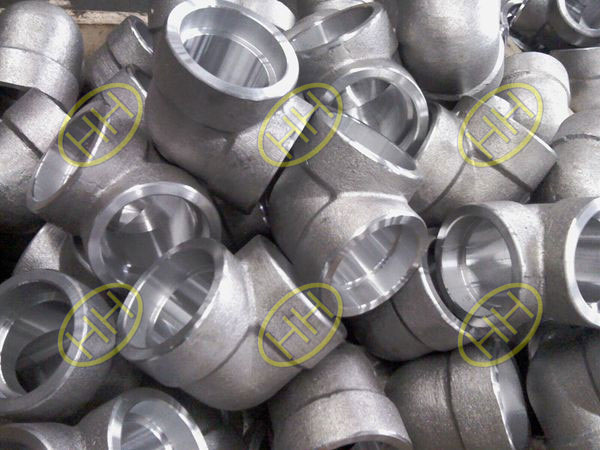
ASTM A182 F347H Pipe Fittings In Haihao Group
3. The influence of temperature on ductile fracture
In the high-temperature plastic forming process of forgings, as the deformation temperature increases, the rheological resistance and tensile strength of the material will decrease, otherwise it will increase. In terms of micro-deformation, physical processes such as dislocation slip and shear, dynamic recrystallization and recovery, phase transformation, etc. within the material will be affected by the forming temperature. The increase in temperature will promote grain growth and will also make The thermal activation energy rises, and ultimately affects the degree of damage and the fracture process during the deformation of the material through the deformation behavior of the microstructure.